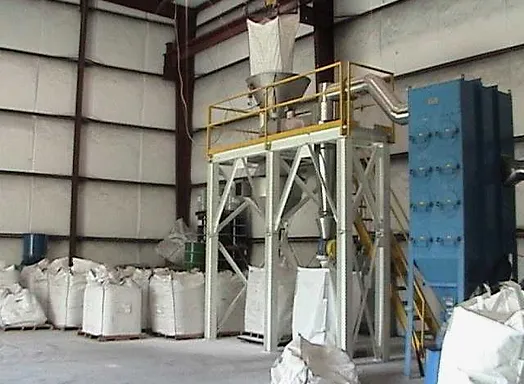
Toll Grinding & Toll classifying
Toll grinding and toll classifying at the finest end of powder grinding is the speciality of Multi-Mineral Processing LLC
We offer toll services for a variety of industrial materials (talc, graphite, mica, zeolithe,…) as well as for other materials. These are produced upon client request in the range of several kilograms all the way up to hundreds of tons.
All our grinding units have been adapted to enable exact cleaning of the parts in direct contact with the material, this starts in the feeding area and continues all the way to the packaging nozzle.
Appropriate equipment for the handling of bulk material like valve packaging machines, big bag-filling stations, pallet press, wrapping machine and good storage facilities, completes MMP’s broad customer service. Our spiral jetmills offer fine grinding with reproducible quality at the highest level!
WHO WE ARE
New Technologies define New Standards
We at Multi Mineral Processing LLC are consultant and specialists in the field of dry fine grinding of organic materials as well as soft to medium-hard industrial minerals with a high aspect ratio.
Micronized industrial minerals such as Talc, Mica, Graphite, Zeolite, Wollastonite, Barite or Micaceous Iron Oxide are main components of plastics, papers, paints, cosmetics, pharmaceuticals and many other products of the daily life influencing their required properties.
Besides the type of material also the particle size and the particle shape described by the aspect ratio have a substantial influence on the properties of the specific final product.
As consumers demand higher quality products, product developers are put under increasing pressure to develop materials that perform better, therefore customers are looking to mineral fillers and functional additives to give the required results.
In this field we are one of the leading companies in the field of dry grinding and classifying of industrial minerals to the finest end.
We have set new standards both in energy efficiency as well as fineness to reach the natural given limits in dry material processing.
All machines have the integrated dynamic classifier. Mounted on our in house developed high-speed motor we have classifier disks made of high strength aluminum alloy to allow circumferential speeds of up to 190 m/s.
With these products a fineness down to the low micrometer range and depending on the material even below 1 µm can be achieved.
With the newly developed EEU System “Enhanced Energy Utilization” the specific energy consumption could be reduced by up to 30 % compared to other micronizing equipment.
For customers, who have capacity constraints or want to produce samples for a new market approach, we offer the possibility to grind larger amounts of raw material with our industrial sized spiral Jetmill in our Toll Processing Plant to the necessary fineness followed by packaging according to customer requirement
Our service:
· Fine grinding with Spiral Jetmills · Fine classifying under overpressure · Quick and clean product changes · Packaging on demand · Storage and transport logistics · Trusted partner in developing new products · Reliable partner in setting up new supply chains · Optimized selection of grinding unit |
Your benefits:
· Extension of product range · Bridge production bottlenecks · Highest product quality · Exact overview of costs · No investment costs · No operating costs · Calculable market launch · High flexibility
|
Grinding / classifying Trials
Trial opportunities in our Testing Center
For the development of new products, it is necessary to test the material properties of grinded or classified products.
Our pilot plant is used to produce product samples for trial applications. We are able to produce anything from 10 kg to 10 to, there is a suitable grinding unit for any possible production batch.
The determined data creates the base line for all successful development of our client products.
The data from these trials, also allows us to plan and offer a spiral jetmill plant, which meets the customer requirements in the areas capacity, raw material specifications and product requirement.
Our laboratory is equipped with the most important measuring and testing units within bulk techniques, rounds off our services in the area of product trials.
In addition to our qualified support during trials our clients appreciate our flexibility as service provider.
We develop wanted target products together with our clients for our clients.
APPLICATIONS
Functional minerals allow special applications due to highest fineness and aspect ratios.
Research and experience in the grinding, classifying and separating technology, which we have gathered over years, made us to experts in the fine powder production.
Based on our technical know-how we have been chosen as partner for many engineering projects. We offer support in both process engineering for dry micronizing plants as well as in the development of special micronized products with enhanced functional properties.
Micronized industrial minerals such as Talc, Mica, Graphite, Zeolite, Wollastonite, Chalk or Barite are main components of plastics, papers, paints, cosmetics, pharmaceuticals and many other products of daily life, these minerals influence the required properties of these day to day products.
Besides the type of material, the particle size and particle shape described by the aspect ratio has a substantial influence on the properties of the finished product. Fineness and aspect ratio define filler functionality and additionally influence the mechanical properties, as well as a number of other features.
Our grinding and classifying technology has been developed and optimized for precisely this purpose: finest grinding while maintaining the high aspect ratio.
Spiral Jetmills comminute the feed material smoothly and maintain existing grain structures, e.g. flaky feed material maintains flaky or aspect ratio is significantly increased due to delamination effects of layered structures.
Furthermore, high classifying speed allows to achieve products with a fineness even below 1 micron. The classifying Rotor-Motor-Unit is placed directly in the heart of the milling chamber. The integration prevents from over-milling and unwanted milling of particles which are already fine enough.
That combination provides finest products with high aspect ratio and a narrow particle size distribution, i.e. with low content of fines and well defined top cut, which are essential requirements for various applications. Talc, for example, needs a distinct flaky shape to achieve the demanded reinforcement in plastics. Barrier effects and excellent embedding of Micaceous Iron Oxide in corrosion protection coatings would not be possible if the lamellar structure of the Micaceous Iron Oxide would have been destroyed. The higher the aspect ratio of Mica in a GRP compound is, the lower the risk is of warpage in the final product.
As consumers demand higher quality products, product developers are put under increasing pressure to develop materials that perform better, therefore developers are looking to mineral fillers and functional additives to give the required results. Application management serves as a link between development, production, quality control, sales and consumers.
In cooperation with our customers we develop innovative solutions in order to consider processing possibilities at a very early point in the product development. Individual, customer-orientated processing solutions include economical and quality aspects in order to guarantee our common success.